內容目錄
鑄件廣泛應用于工業制造中,如汽車零部件、機械設備、航空航天裝置等。由于鑄造工藝的特性,鑄件表面通常覆蓋著油脂、氧化皮、砂屑和其他殘留物,這些污染物不僅影響鑄件的表面質量,還可能對后續加工和涂裝工藝產生負面影響。因此,鑄件清洗是生產流程中不可或缺的一環。在眾多清洗方法中,超聲波清洗機因其高效、無損的特點,在鑄件清洗領域得到了廣泛應用。
一、鑄件清洗的挑戰與需求
鑄件的清洗具有獨特的挑戰性。首先,鑄件通常具有復雜的幾何形狀和內部結構,傳統的清洗方法難以徹底清除內外表面的污染物。其次,鑄件表面的油脂、氧化皮和砂屑等污染物種類多樣,清洗難度較大。最后,鑄件通常需要在清洗后進行進一步加工或涂裝,因此清洗工藝必須確保表面無殘留物,且不會損傷基材。
這些挑戰要求清洗方法不僅要具有較強的去污能力,還要能夠在不損傷鑄件表面的前提下,達到高效、全面的清潔效果。超聲波清洗機通過其獨特的工作原理和工藝組合,能夠有效滿足這些需求。
二、超聲波清洗機的工作原理及其在鑄件清洗中的優勢
超聲波清洗機通過高頻振動在清洗液中產生空化作用,空化氣泡在破裂時釋放出局部高溫高壓,從而對鑄件表面的污染物進行剝離和分解。與傳統的機械清洗方法相比,超聲波清洗具有以下顯著優勢:
- 高效徹底:超聲波清洗可以深入鑄件的復雜幾何結構和內部通道,對細小的孔洞、縫隙和盲孔進行全方位清潔。
- 無損清洗:超聲波清洗的物理作用力溫和,能夠有效去除污染物,而不會損傷鑄件的表面。
- 適用廣泛:超聲波清洗機可以處理各種材質和類型的鑄件,包括鋼鐵、鋁合金、銅合金等。
三、適用于鑄件清洗的清洗劑類型及其選擇
為了增強超聲波清洗的效果,通常需要結合適當的清洗劑。清洗劑的選擇應根據鑄件材質和表面污染物的性質進行優化。以下是幾種常用的清洗劑類型及其在鑄件清洗中的應用:
1. 堿性清洗劑
堿性清洗劑通常用于去除鑄件表面的油脂、油污和有機物。這類清洗劑含有氫氧化鈉、碳酸鈉等堿性成分,能夠有效分解和乳化油脂類污染物。堿性清洗劑適用于清洗鋼鐵和鋁合金鑄件,但在清洗鋁材時需要控制清洗劑的堿性強度,以避免腐蝕。
2. 酸性清洗劑
酸性清洗劑主要用于去除鑄件表面的氧化皮、銹跡和水垢。常用的酸性成分包括磷酸、檸檬酸和鹽酸。酸性清洗劑能夠通過與金屬氧化物反應,將其溶解,從而去除表面的銹跡和氧化層。酸性清洗劑適用于清洗鋼鐵鑄件,但需要注意防止酸性對基材的過度腐蝕。
3. 中性清洗劑
中性清洗劑具有溫和的化學性質,適用于對表面要求較高且容易受腐蝕的鑄件材料,如銅合金和某些鋁合金。中性清洗劑通常用于去除表面的灰塵、輕度油脂和氧化物,不會對鑄件表面造成損傷。
4. 除銹清洗劑
對于嚴重銹蝕的鑄件,使用專門的除銹清洗劑是必要的。這類清洗劑含有特殊的化學成分,能夠有效溶解和去除銹跡,并能在清洗后形成保護膜,防止鑄件表面再次生銹。除銹清洗劑通常在清洗鋼鐵鑄件時使用。
5. 環保型清洗劑
隨著環保要求的提高,越來越多的企業傾向于使用環保型清洗劑。這類清洗劑不含有害物質,能夠有效去除鑄件表面的污染物,同時減少對環境的影響。環保型清洗劑適用于各種鑄件的清洗,特別是在對操作安全和環境友好性要求較高的情況下。
四、超聲波清洗鑄件的工藝流程與注意事項
在使用超聲波清洗機清洗鑄件時,合理的工藝流程和操作注意事項可以顯著提升清洗效果和效率。
1. 前處理
在進行超聲波清洗之前,通常需要對鑄件進行預處理,如去除表面的粗大污物或用溶劑清洗掉大量油脂。這一步驟能夠減少超聲波清洗機的負荷,延長清洗液的使用壽命。
2. 清洗參數的優化
根據鑄件的材質、污染物類型和清洗劑的性質,合理設置超聲波清洗機的工作參數,包括超聲波頻率、功率、清洗時間和溫度。通常,頻率越高,清洗精度越高;功率越大,清洗速度越快。清洗時間和溫度應根據具體情況調節,以保證最佳清洗效果。
3. 清洗劑的使用與維護
在清洗過程中,應嚴格按照清洗劑的使用說明控制其濃度,并定期更換清洗液,以防止污染物積累影響清洗效果。對于易揮發或有腐蝕性的清洗劑,需采取相應的安全措施,如通風、佩戴防護裝備等。
4. 后處理與干燥
清洗后,應及時對鑄件進行漂洗,去除殘留的清洗劑,然后進行干燥處理,以防止水分殘留引起銹蝕。對于特別精密或對表面要求高的鑄件,還可以進行防護處理,如噴涂防銹油或涂層。
五、總結
超聲波清洗機在鑄件清洗中表現出顯著的優勢,能夠高效去除復雜結構和微小細節中的污染物。然而,清洗效果的好壞不僅取決于超聲波設備的性能,還與所選用的清洗劑密切相關。通過合理選擇和使用清洗劑,如堿性清洗劑、酸性清洗劑、中性清洗劑和環保型清洗劑等,可以有效應對鑄件表面的油污、銹跡和氧化皮等難題。合理的清洗流程和操作注意事項同樣至關重要,可以確保鑄件清洗的高質量和高效率。
了解和掌握這些要素,不僅能夠提升鑄件的表面質量,滿足后續工藝的要求,還能降低清洗過程中的能源消耗和環境影響,從而實現更高效、更環保的鑄件生產流程。
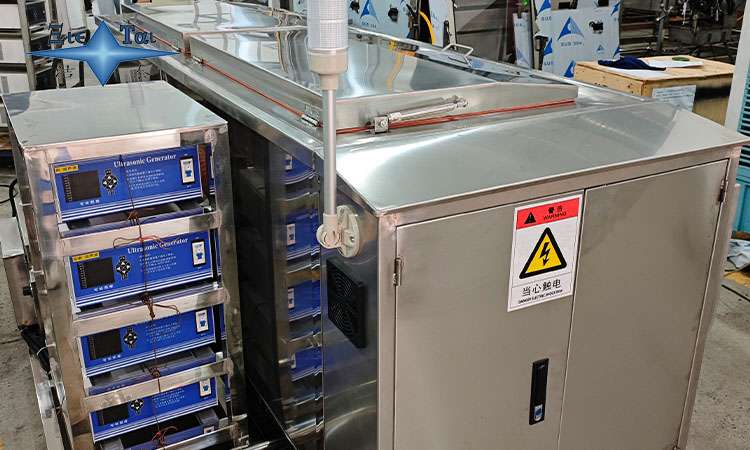